V-PROCESS CASTING
The V-Process Advantage
The V-Process adds value to your initiatives by helping bring projects from concept through prototype, and into full production.
Key Features and Benefits:
- Speed To Market
- 150 RMS Finish
- Excellent Casting Integrity
- Corrosion Resistant
- Zero Degree Draft
- Thin Walls
- Quick Pattern Revision
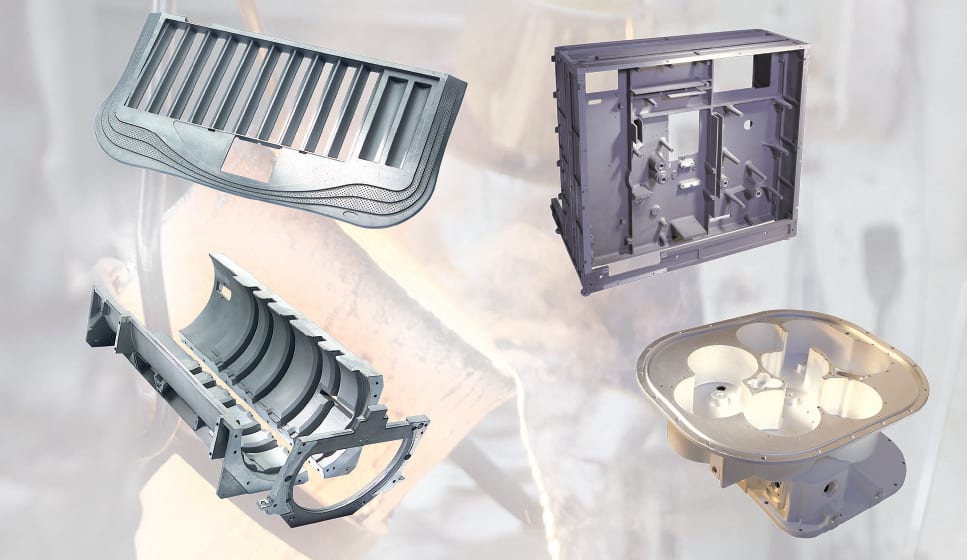
V-PROCESS Sequence
The V-Process is a crossover process, which combines the best benefits from all other standard casting processes.
When considering:
- speed to market,
- zero draft,
- initial investment,
- repeatability,
- surface finish,
- and structural integrity
The V-process can provide a one-stop solution for casting projects from prototype through full production.

The pattern (with vent holes) is placed on a hollow carrier plate.
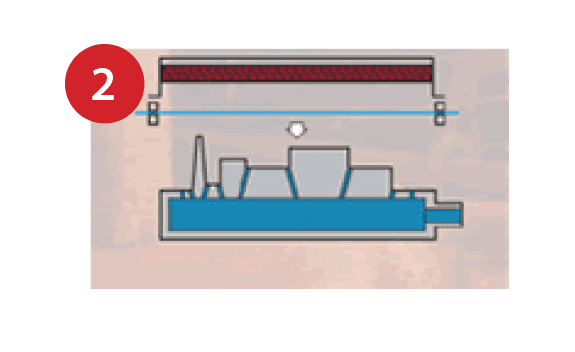
A heater softens the .003” to .008” plastic film. Plastic has good elasticity and a high deformation ratio.
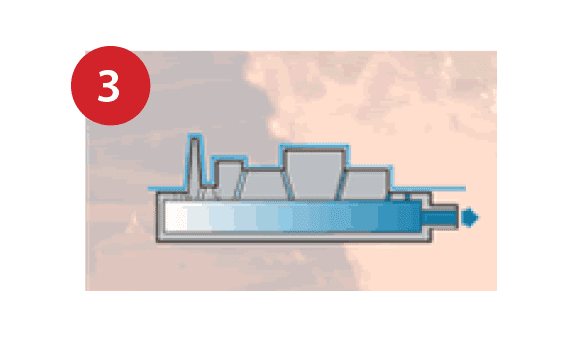
Softened film drapes over the pattern with 200 to 400 mm Hg vacuum acting through the pattern vents to draw it tightly around the pattern.
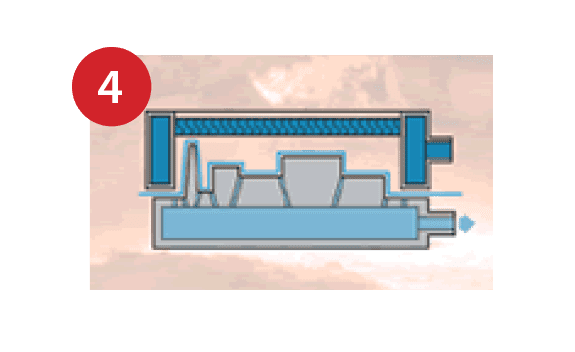
The flask is placed on the film-coated pattern. Flask walls are also a vacuum chamber with the outlet shown at right.
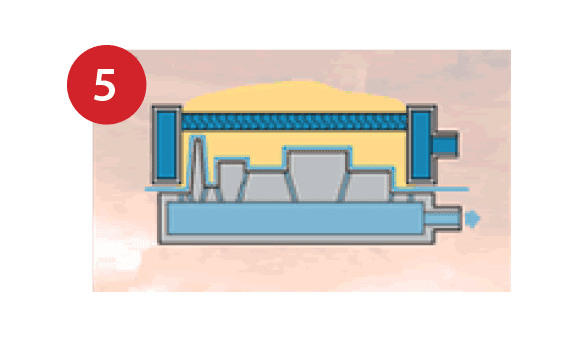
The flask is filled with dry, unbonded sand. A slight vibration compacts sand to maximum bulk density.
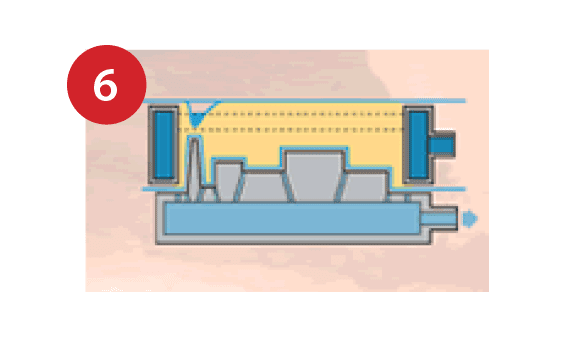
A sprue cup is formed and the mold surface leveled. The back of the mold is covered with unheated plastic film.
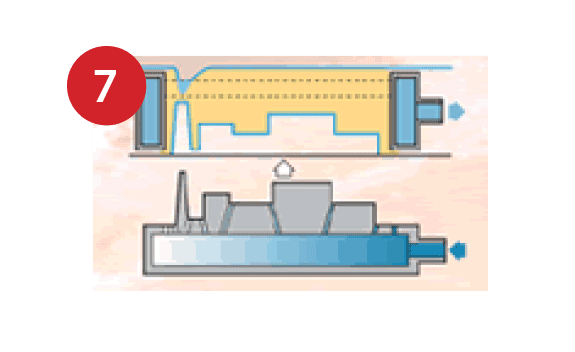
Vacuum is applied to the flask. Atmospheric pressure then hardens the sand. The vacuum is released, pressurized air is introduced into the carrier and the mold is stripped.
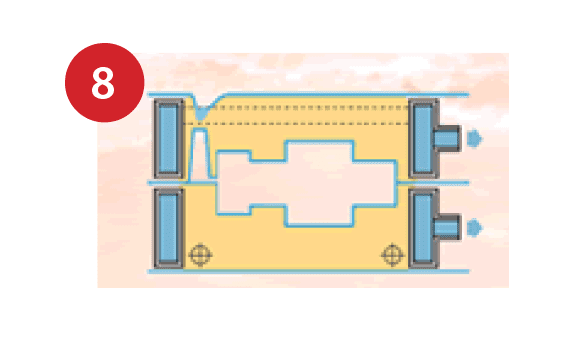
The cope and drag assembly forms a plastic- lined cavity. During pouring, molds are kept under vacuum.
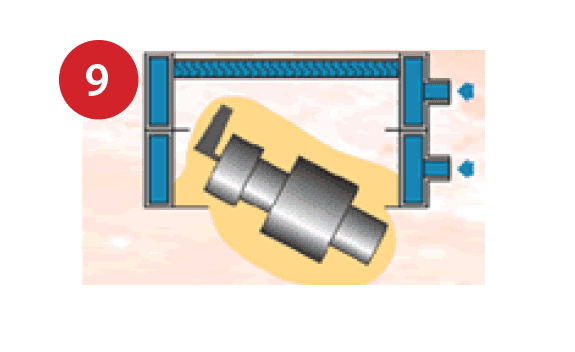
After cooling, the vacuum is released and free-flowing sand drops away leaving a clean casting with no sand lumps. The sand is cooled for reuse.
Our Services
Full Range of Services:
- X-ray (film)
- Spectrograph chemical analysis
- Mechanical testing (yield, tensile and elongation)
- T-51 heat treatment
- T-6 heat treatment
- CMM layout
- Welding
- Additional blasting finishes available
- Machining
- Minor assembly
- Pressure testing
- Die penetrant testing
- Wet and powder painting
- Anodize
- Impregnation
- Others available upon request
Aluminum Castings: Process Comparisons
Process | Typical Size Range | Tolerances | Surface Finish | Min. Draft Required | Min. Section Thickness | Typical Order Quantities | Typical Tooling Costs | Nominal Lead Times |
---|---|---|---|---|---|---|---|---|
V-Process Castings | Up to 150 lbs | ± .010" for the first inch, then add ± .002"per inch. Add a max .020 across parting line | 125-150 RMS | None | .125" | All | $3,000 to $14,000 | Samples: 2 to 3 weeks Production: 4 weeks after approval |
Sand Castings | Ounces to tons | ± 1/32" to 6", then add ± .003" per inch. Add a ± .020" to .090" across parting line. | 200-550 RMS | 1 to 5 degrees | .25" | All | $800 to $4,000 | Samples: 2 to 6 weeks Production: 2 to 6 weeks after approval |
Investment (Lost Wax) Castings | Ounces to 20 lbs | ± .003" to 1/4", ± .004" to 1/2", ± .005" to 3",then add ± .003" per inch. | 63-125 RMS | None | .060" | Under 1000 | $3,000 to $20,000 | Samples: 8 to 10 weeks Production: 5 to 12 weeks after approval |
Permanent Mold Castings | Ounces to 100 lbs | ± 0.15" to 1", then add ± .002" per inch. Add ± .010" to .030" across parting line. | 150-300 RMS | 2 to 5 degrees | .1875" | 500+ | $5,000 to $25,000 | Samples: 8 to 20 weeks Production: 10 to 12 weeks after approval |
Plaster Mold Castings | Ounces to 50 lbs | ± .005" to 2", then add ± .002" per inch. Add ± .010" across the parting line. | 63-125 RMS | 1/2 to 2 degrees | .070" | Prototypes up to 250 | $3,000 to $15,000 | Samples: 2 to 10 weeks Production: 4 to 8 weeks after approval |
Die Castings | Ounces to 15 lbs | ± .002" per inch. Add ± .015" across parting line. | 32-63 RMS | 1 to 3 degrees | .030" to .060" | 2500+ | $10,000 to $100,000 | Samples: 12 to 22 weeks Production: 8 to 14 weeks after approval |